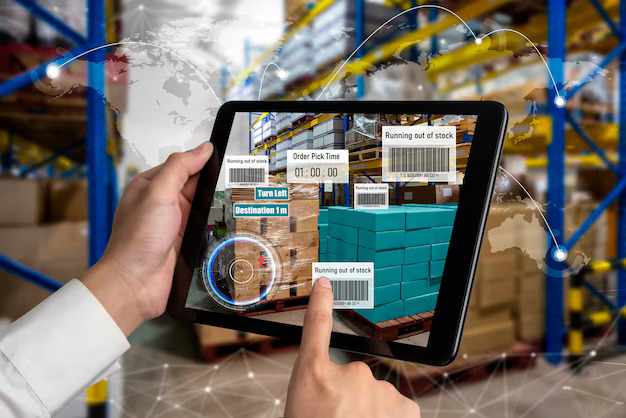
In the competitive world of electrical manufacturing, customer satisfaction is a top priority. As product complexity increases and expectations rise for speed, accuracy, and quality, businesses must adopt intelligent solutions to stay ahead. One of the most impactful tools in this transformation is Electrical Manufacturing ERP Software. An ERP (Enterprise Resource Planning) system integrates every function in the business—from design to delivery—ensuring smooth operations and, most importantly, a superior customer experience.
Let’s explore how ERP software for the electrical manufacturing industry plays a vital role in boosting customer satisfaction at every stage.
Streamlining Order Management with Electrical Manufacturing ERP Software
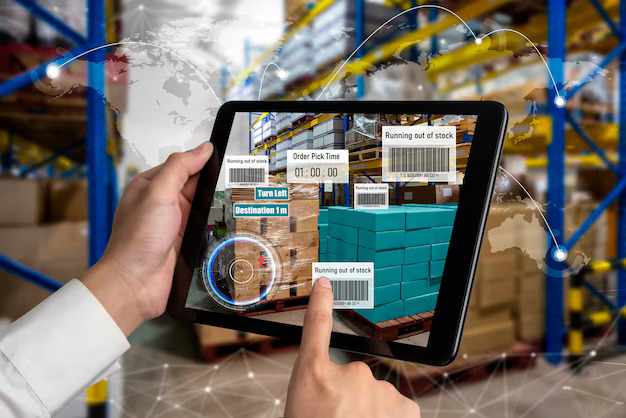
A customer’s journey often starts with placing an order. How efficiently that order is processed sets the tone for the entire relationship. Manual systems or disconnected software can lead to delays, mistakes, and miscommunications. This is where a robust Electrical Manufacturing ERP comes in.
With an ERP system, the order process becomes streamlined. Sales teams can instantly check inventory levels, manufacturing capacity, and delivery timelines. This transparency helps in setting accurate expectations for customers from the beginning. As all data is centralized, teams across departments—from procurement to production—have access to real-time updates.
Moreover, automation features within ERP reduce the chances of human error. Whether it’s creating invoices or generating purchase orders, the software ensures accuracy and consistency. Faster order processing and fewer mistakes directly translate into happier customers.
Enhancing Product Quality with ERP Software for Electrical Manufacturing Industry
Customers care about quality. Delivering a product that meets technical specifications consistently is key to winning and keeping customer trust. ERP software for electrical manufacturing industry enables manufacturers to embed quality control at every step of production.
With quality management modules built into the ERP system, manufacturers can set up checkpoints throughout the production cycle. These checkpoints ensure that raw materials meet the required standards and that each assembly phase adheres to strict specifications. Any deviation can be flagged immediately, allowing for swift corrective actions.
Additionally, ERP systems allow manufacturers to track and analyze quality data over time. If patterns of defects emerge, manufacturers can identify root causes and take preventive measures. Over time, this leads to fewer reworks, less scrap, and, most importantly, more consistent quality, which customers value immensely.
Improving On-Time Delivery through Cloud-Based Electrical Manufacturing ERP Software
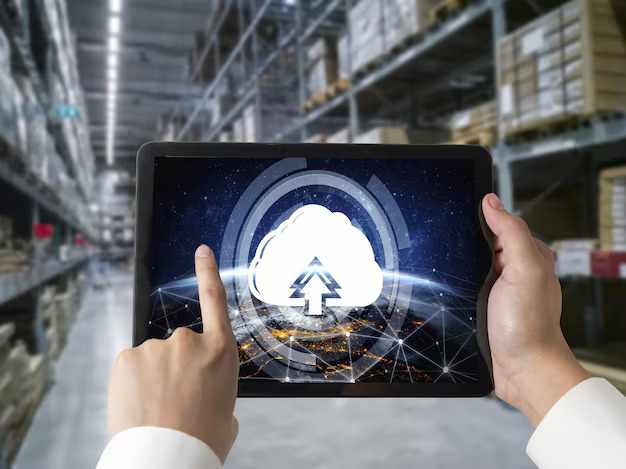
In today’s fast-paced world, customers expect timely delivery—every single time. Delays can damage trust and lead to lost business. Cloud-based electrical manufacturing ERP software ensures production schedules, procurement plans, and logistics are all tightly integrated and optimized for on-time delivery.
These ERP systems use predictive analytics and smart planning features to forecast demand and adjust production accordingly. They also alert managers to supply chain disruptions or machine downtimes before they impact delivery timelines. By proactively managing potential bottlenecks, manufacturers can maintain consistent production flow.
Furthermore, because cloud-based systems offer real-time data access from anywhere, decision-makers can resolve issues quickly, even remotely. This flexibility and speed help prevent delays, keeping customers satisfied with reliable, on-schedule deliveries.
Increasing Transparency and Communication with Customers
Communication is a pillar of customer satisfaction. Clients appreciate being kept in the loop about their order status, lead times, and any potential delays. Electrical Manufacturing ERP software provides tools for better communication, both internally and externally.
With ERP, manufacturers can generate real-time reports and share order tracking information directly with clients. Customers no longer need to wait for phone calls or emails—they can access portals to see updates on their orders anytime. This transparency builds trust and reduces anxiety.
Internally, ERP fosters better collaboration between departments. Sales, customer service, and production teams work from the same data source, so everyone has up-to-date information. When a customer calls with a query, they get accurate answers quickly, which boosts confidence and satisfaction.
Personalizing Customer Service with Electrical Manufacturing ERP Capabilities
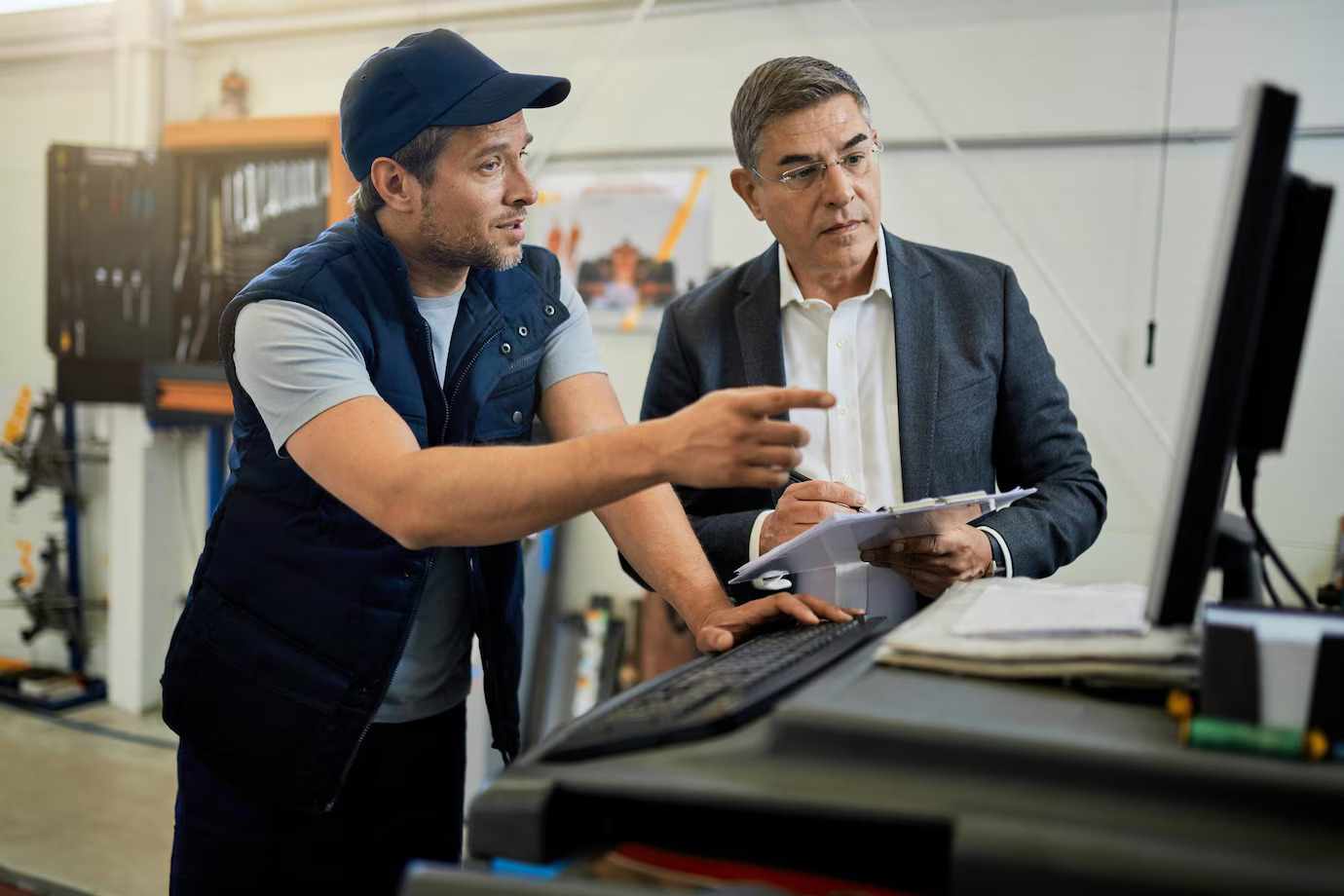
ERP systems do more than manage operations—they also collect valuable customer data. This data can be used to tailor services and offerings, giving customers a more personalized experience. For example, ERP software can track buying patterns, product preferences, and order history.
With this information, sales and service teams can recommend relevant products or proactively offer support. If a customer has a recurring need, the ERP system can even set up automated reorders or reminders. This level of personalization shows that the manufacturer understands the customer’s business and is invested in their success.
Additionally, ERP systems help manage warranties, service contracts, and support tickets—all from a single platform. When customers receive fast, informed service after a sale, their satisfaction increases, and long-term loyalty is strengthened.
Driving Continuous Improvement with Insights from Electrical Manufacturing ERP
To maintain high levels of customer satisfaction, businesses need to evolve continuously. Cloud-based ERP solutions provide powerful dashboards and analytics tools that help manufacturers monitor performance across operations.
Metrics like delivery timelines, production efficiency, customer feedback, and complaint resolution times are easily trackable. These insights allow manufacturers to identify trends and address issues before they impact customer satisfaction. Continuous improvement becomes part of the culture.
For example, if data shows frequent delays with a specific component supplier, procurement teams can switch vendors before customer orders are affected. If a particular product line receives more service complaints, engineers can investigate and refine the design. These proactive adjustments improve reliability, reduce dissatisfaction, and show customers that the manufacturer is committed to excellence.
Why TheERPHub is Your Ideal Partner for Electrical Manufacturing ERP Solutions
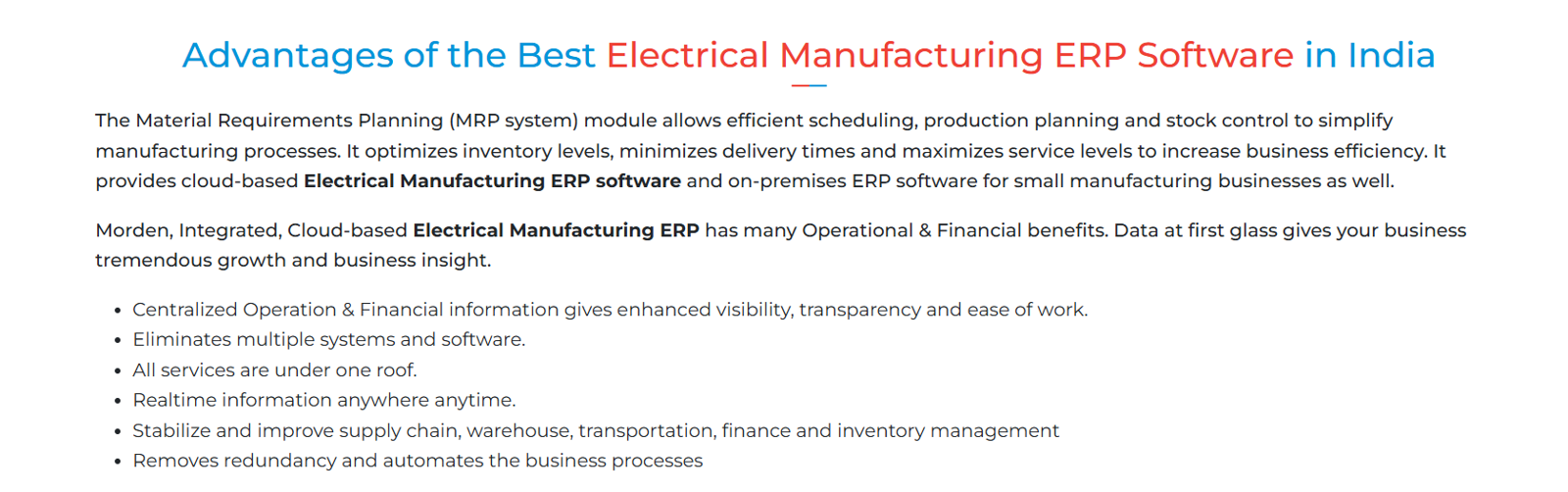
In the electrical manufacturing industry, where precision, speed, and service matter most, ERP software is not just a back-end tool—it’s a strategic asset. From ensuring accurate orders and superior quality to guaranteeing on-time delivery and proactive customer care, an ERP system shapes the entire customer experience.
TheERPHub specializes in providing tailored cloud-based electrical manufacturing ERP software designed to meet the unique challenges of your industry. With years of experience, user-friendly interfaces, and scalable solutions, TheERPHub empowers electrical manufacturers to deliver outstanding service and exceed customer expectations.
Ready to enhance your customer satisfaction and business performance? Contact us today for a free demo and consultation.
Write a comment ...